Porosity in Welding: Identifying Common Issues and Implementing Ideal Practices for Avoidance
Porosity in welding is a pervasive issue that frequently goes undetected till it triggers considerable problems with the honesty of welds. This usual flaw can jeopardize the stamina and longevity of bonded frameworks, positioning safety threats and causing expensive rework. By understanding the source of porosity and implementing reliable prevention strategies, welders can dramatically enhance the quality and integrity of their welds. In this discussion, we will certainly check out the key variables adding to porosity development, examine its destructive impacts on weld efficiency, and go over the most effective methods that can be adopted to decrease porosity incident in welding procedures.
Typical Root Causes Of Porosity
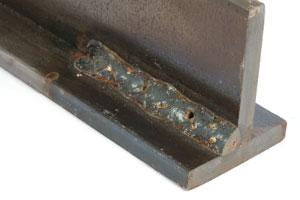
Using unclean or damp filler materials can present pollutants into the weld, contributing to porosity problems. To minimize these common causes of porosity, comprehensive cleaning of base metals, proper shielding gas option, and adherence to optimal welding specifications are important techniques in accomplishing top quality, porosity-free welds.
Influence of Porosity on Weld High Quality

The presence of porosity in welding can dramatically jeopardize the architectural stability and mechanical homes of bonded joints. Porosity develops spaces within the weld steel, compromising its total stamina and load-bearing ability. These voids work as tension focus points, making the weld extra prone to breaking and failure under used loads. Furthermore, porosity can lower the weld's resistance to corrosion and various other ecological factors, additionally diminishing its durability and performance.
Welds with high porosity degrees have a tendency to display reduced effect stamina and reduced ability to flaw plastically prior to fracturing. Porosity can hamper the weld's capability to efficiently transmit pressures, leading to early weld failure and prospective security hazards in critical frameworks.
Finest Practices for Porosity Prevention
To enhance the architectural stability and quality of bonded joints, what certain procedures can be implemented to lessen the incident of porosity during the welding procedure? Porosity prevention in welding is essential to make certain the stability and strength of the last weld. One efficient practice appertains cleaning of the base steel, eliminating any pollutants such as rust, oil, paint, or wetness that might cause gas entrapment. Guaranteeing that the welding equipment remains in good problem, with clean consumables and proper gas flow prices, can also considerably minimize porosity. Additionally, keeping a stable arc and controlling the welding criteria, such as voltage, present, and travel speed, helps develop a constant weld swimming pool that lessens the threat of gas entrapment. Utilizing the correct welding strategy for the certain product being welded, such as changing the welding angle and gun setting, can further stop porosity. he said Regular evaluation of welds and instant remediation of any type of concerns recognized during the welding procedure are essential methods to avoid porosity and produce top notch welds.
Importance of Proper Welding Techniques
Executing correct welding methods is paramount in making certain the structural stability and quality of bonded joints, building upon the structure of effective porosity avoidance steps. Too much heat can lead to raised porosity article source due to the entrapment of gases in the weld pool. In addition, using the ideal welding parameters, such as voltage, existing, and take a trip speed, is vital for achieving audio welds with marginal porosity.
Moreover, the choice of welding procedure, whether it be MIG, TIG, or stick welding, should straighten with the specific demands of the task to ensure optimum results. Appropriate cleansing and preparation of the base metal, along with selecting the ideal filler product, are also necessary components of proficient welding methods. By sticking to these best methods, welders can lessen the threat of porosity development and produce high-grade, structurally sound welds.
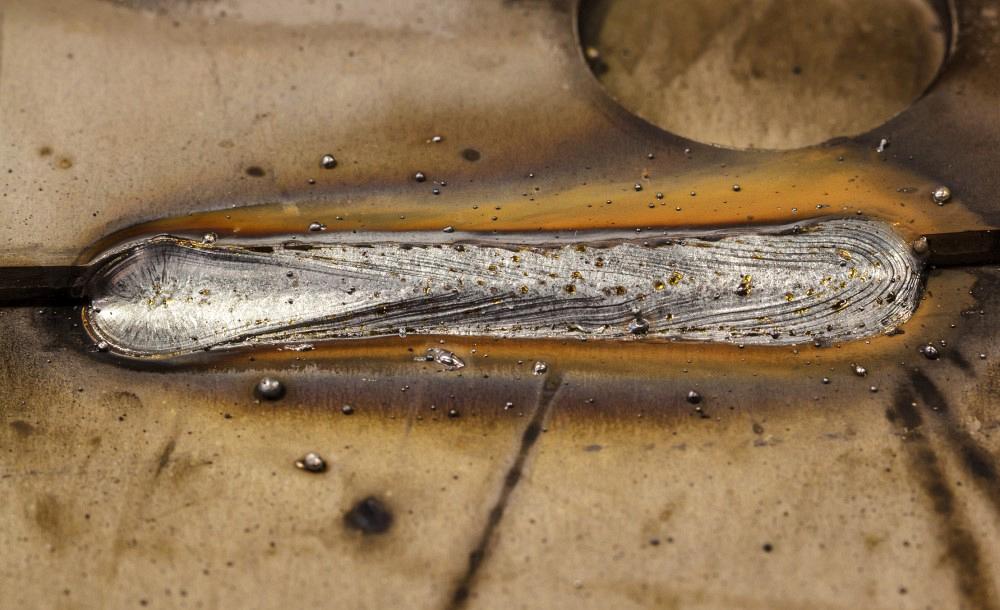
Examining and Quality Control Steps
Quality assurance measures play a crucial function in confirming the honesty and reliability of welded joints. Checking treatments are important to discover and stop porosity in welding, making certain the strength and resilience of the see here end product. Non-destructive screening approaches such as ultrasonic screening, radiographic screening, and aesthetic inspection are commonly employed to determine prospective flaws like porosity. These methods permit the analysis of weld top quality without endangering the stability of the joint. What is Porosity.
Post-weld inspections, on the other hand, analyze the final weld for any type of issues, including porosity, and verify that it fulfills specified requirements. Applying a comprehensive high quality control strategy that includes extensive screening treatments and evaluations is vital to lowering porosity issues and guaranteeing the general high quality of bonded joints.
Verdict
In conclusion, porosity in welding can be a typical problem that affects the top quality of welds. By identifying the common reasons for porosity and executing finest techniques for avoidance, such as correct welding techniques and screening measures, welders can make certain excellent quality and dependable welds. It is necessary to focus on avoidance techniques to lessen the event of porosity and keep the honesty of bonded structures.